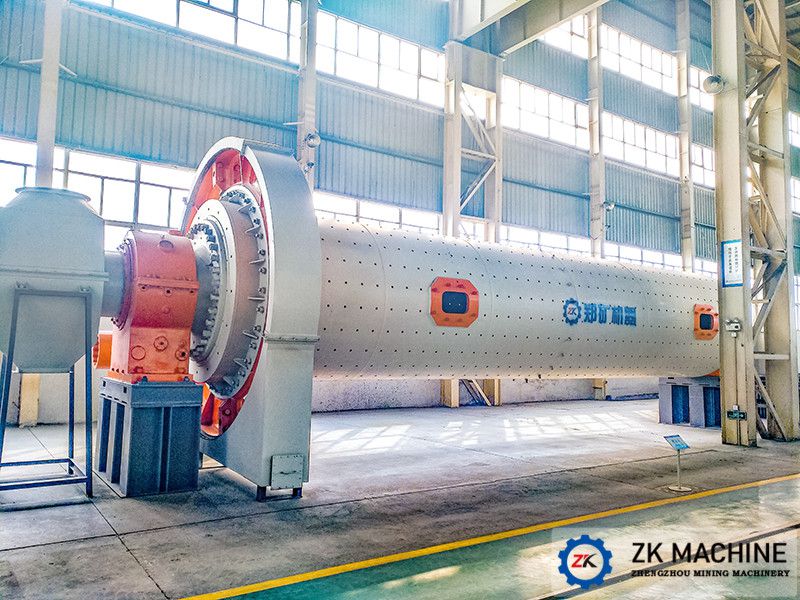
(1) Classification according to the shape of grinding media loaded in the mill
1. Ball mill
The grinding media loaded in the mill is mainly steel balls or steel segments. This kind of mill is most commonly used.
2. Rod mill
The mill is loaded with steel rods with a diameter of 50-100mm as grinding media. The ratio of the length and diameter of the barrel of the rod mill is generally 1.5-2.
3. Baseball mill
This mill usually has 2-4 bins. A cylindrical steel rod is loaded as the grinding medium in the first bin, and steel balls or steel segments are loaded in the subsequent bins. The length-to-diameter ratio of the baseball mill should be about 5, the ratio of the length of the bar warehouse to the effective diameter of the mill should be between 1.2-1.5, and the length of the bar is about 100mm shorter than the bar warehouse to facilitate the parallel arrangement of the steel rods to prevent crossovers and Messy.
(2) Classification according to discharge method
1. Tail unloading mill
The material to be ground is fed from one end of the mill and discharged from the other end. It is called tail unloading mill.
2. Intermediate unloading mill
The material to be ground is fed from both ends of the mill and discharged from the middle of the barrel of the mill. It is called an intermediate unloading mill. This type of mill is equivalent to two ball mills used in parallel, so the equipment is compact and the process is simplified.
(3) Classification by transmission mode
1. Center Drive Mill
The motor drives the hollow shaft of the discharge end of the mill through the reducer to drive the mill to rotate. The output shaft of the reducer is on the same line as the center line of the mill.
2. Edge drive mill
The motor drives the large cylinder fixed on the discharge end cylinder through the reducer to drive the mill cylinder to rotate.
(4) Other classifications
According to the process operation, it can be divided into dry mill, wet mill, intermittent mill and continuous mill. Compared with intermittent mills, continuous mills have higher output, lower power consumption per unit weight, higher degree of mechanization, and fewer operators, but the capital investment costs are large, and operation and maintenance are complicated. At present, intermittent mills are rarely used and are often used as experimental mills.