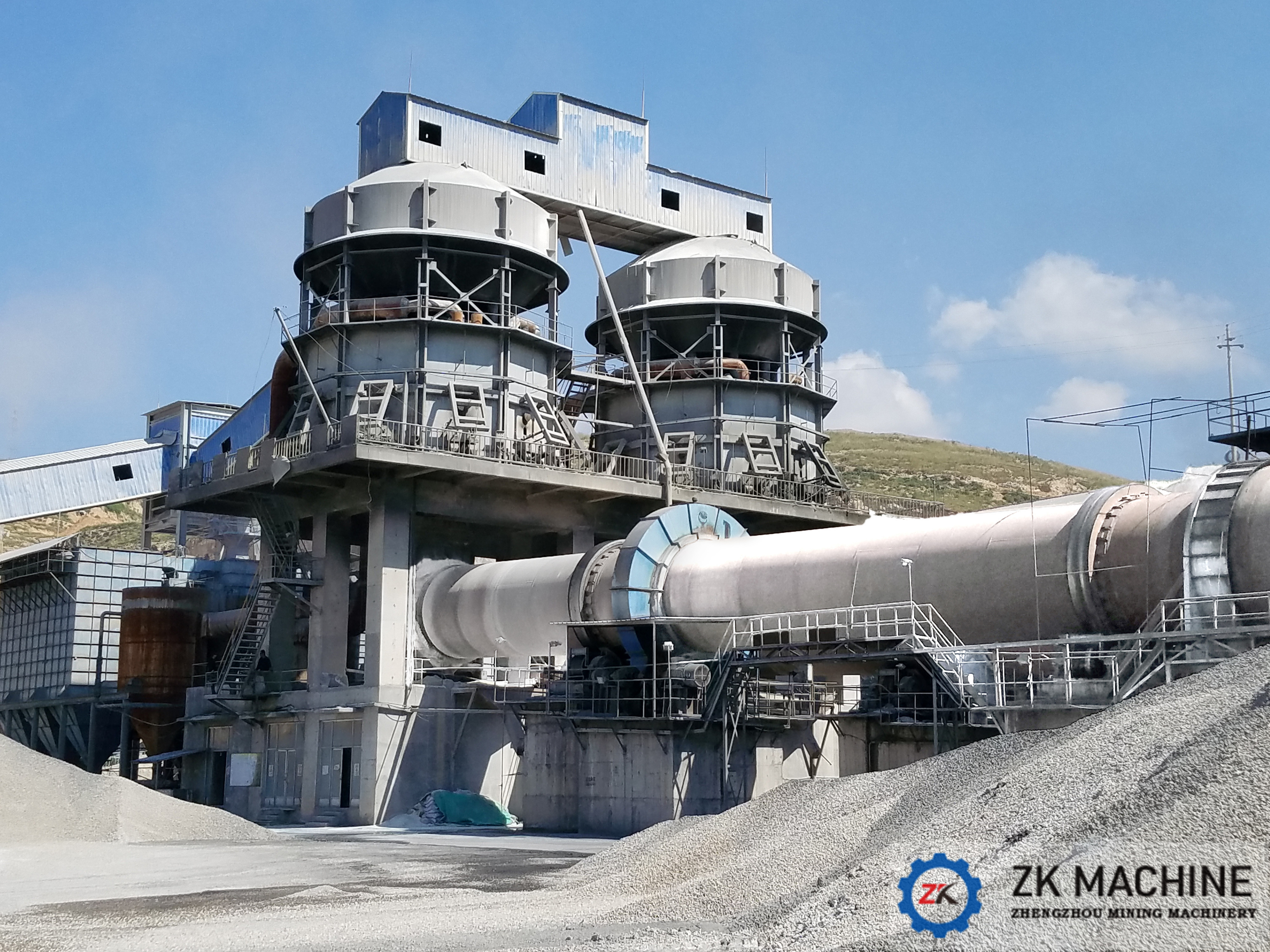
Quicklime Rotary Kiln is mainly used for calcinating quicklime and light-burned dolomite which are used in iron and steel factory and ferroalloy factory. Use the gas that pollutes the environment as the main energy source, turn waste into treasure, and thoroughly treat the pollution of the earth-burning kiln. The environment can be protected, the quality is good, and the cost is low.
The use of quicklime to make steel slag has a fast speed, which can improve the desulfurization and phosphorus efficiency (about 10%), also can shorten the smelting time (about 2~4 minutes), save lime and fluorite consumption (reduce 10~40%), and improve the yield of molten steel. Yield (about 1.5%), reduce fuel consumption (5-8 kg/ton), and extend lining life (over 20%). Rotary kiln produces stable quicklime, which is beneficial to realize automatic control of steelmaking process. The quicklime rotary kiln system designed and manufactured by our company has been widely used in many iron and steel enterprises, and has been promoted in other fields such as nonferrous metals, chemical industry, desulfurization, calcium carbide, papermaking and so on.
The advantages of Quicklime Rotary Kiln
1. The rotary kiln is an open-type calcination, the kiln body structure is simple, the gas flow is smooth, the sulfur-containing flue gas can be discharged in time, the sulfur in the fuel is not easy to adhere, so the product has a low sulfur content and meets the requirements of steelmaking. At the same time, the materials are uniformly rolled forward in the kiln, heated evenly, the product quality is stable, and the rate of burning and overburning is very low, and it can be used for calcining high-activity steel-making lime. Under the same conditions, the activity of lime produced by rotary kilns is higher than that of gas-fired kilns, with an average higher than 30ml, and the activity is generally 340-380ml, even as high as 400ml.
2. Rotary kiln can directly calcine 10-50mm fine-grained limestone. Generally, 0-30mm fine-grained limestone accounts for about 30-40% of the total output. This part of limestone cannot be used by other kiln. And with the "refining" of steel raw materials, sintering gradually replaces limestone with quicklime, and fine-grained limestone cannot be comprehensively utilized. The construction of a rotary kiln line can not only make full use of high-quality limestone mine resources, but also conform to the sustainable development policy of the lime industry.
3. The vertical cooler at the kiln outlet can not only quench the high-temperature lime and improve the activity of the product, but also facilitate transportation and storage. At the same time, higher temperature secondary air enters the kiln. It can effectively increase the firing temperature in the kiln and reduce fuel consumption.
4. A vertical preheater is installed at the kiln inlet to make full use of the high-temperature flue gas produced by the calcination in the rotary kiln, to preheat the limestone from ambient temperature to the initial decomposition state. This can not only greatly increase the output of the rotary kiln, but also fully reduce the heat consumption per unit product;
5. The temperature of the flue gas discharged by the vertical preheater at the kiln inlet is low, between 280-350℃. And the dust concentration is low, about 20g/Nm3, which makes the configuration of subsequent flue gas treatment simple and effective, and can smoothly meet the environmental protection requirements.