01
Strengthen production management, strictly control the storage and use of raw and auxiliary materials, reduce the waste of raw and auxiliary materials and the waste generated by the expiration of raw and auxiliary materials. For example, the packaging specifications of purchased chemicals should be miniaturized as much as possible to reduce the disposal of expired chemicals.
02
Eliminate backward production processes and optimize production process technology. For example, paint residue comes from overspray mist that has not effectively formed a coating film. From the perspective of improving the adhesion rate of the paint, the use of a spraying process with high transmission efficiency can control and reduce the amount of paint residue generated from the source. The spraying transmission efficiency of electrostatic atomization, electrostatic rotary cup atomization and electrostatic disc atomization is about 1-1.3 times higher than that of traditional air spraying and paint-free spraying.
03
For various types of waste organic solvents containing benzene, ethers, esters, etc. generated in the production process of chemical, petrochemical, pharmaceutical and other enterprises, if there is a value for reuse, the enterprise can build an organic solvent reuse treatment device to reduce the amount of waste organic solvents to be treated. Common organic solvent recycling and treatment devices include extraction distillation devices, which use the different saturated vapor pressures of organic matter at different temperatures to separate useful organic matter and realize the resource utilization of hazardous waste.
04
For chemical, petrochemical and other enterprises, a large number of various distillation residues will be generated in the production process. For such high-concentration organic waste liquid, due to its high calorific value, enterprises can build RTO, RCO, waste liquid incinerators and other devices to treat the distillation residues produced by themselves, which can avoid the risks in the transportation of hazardous waste.
05
For raw and auxiliary materials with large annual consumption in the production process of chemical, petrochemical and other enterprises, their material packaging barrels are a large source of hazardous waste. Storage tanks can be used instead of packaging barrels. In addition, the structure of the raw material packaging barrel can be optimized, and the packaging barrel can be equipped with an inner lining. After the raw material is used up, only the inner lining needs to be disposed of as hazardous waste. The outer packaging material can be recycled, which can reduce the amount of hazardous waste waste packaging barrels.
06
For paint and coating production enterprises, general equipment manufacturing industry and special equipment manufacturing industry, enterprises that use a large amount of paint have the characteristics of high organic waste gas concentration. Enterprises can adopt activated carbon adsorption/desorption + catalytic combustion integrated treatment device, or zeolite wheel adsorption + catalytic combustion integrated device, etc., instead of regular replacement of activated carbon disposal methods, to reduce the amount of waste activated carbon generated.
07
For chemical enterprises such as paint and ink, whose products are produced in batches, switching to the production of different types of products requires cleaning of equipment containers. For the generated cleaning waste liquid, enterprises can optimize their production management plans, and try to produce the same type of products in the same batch, reduce the number of equipment cleanings, and thus reduce the amount of cleaning waste liquid generated.
08
For machining enterprises, the hazardous waste generated is mainly waste emulsion, etc. Enterprises can increase the filtering device to extend the service life of the emulsion, reduce the replacement frequency, and reduce the amount of hazardous waste waste cutting fluid generated.
09
For waste acid or waste alkali generated in the production process of an enterprise, after physical treatment, chemical treatment, physical and chemical treatment and biological treatment, if it can meet the relevant regulations and emission standards for discharge to environmental water bodies or municipal sewage pipe networks and treatment facilities, it can be treated through wastewater treatment facilities to reduce the final amount of hazardous waste generated by the enterprise.
10
For the dewatered sludge generated by the enterprise's factory wastewater treatment station with a high moisture content, the enterprise can improve the sludge dewatering device, such as adopting a dewatering and drying integrated device to reduce the sludge moisture content to 50%, thereby reducing the amount of dewatered sludge generated by the enterprise.
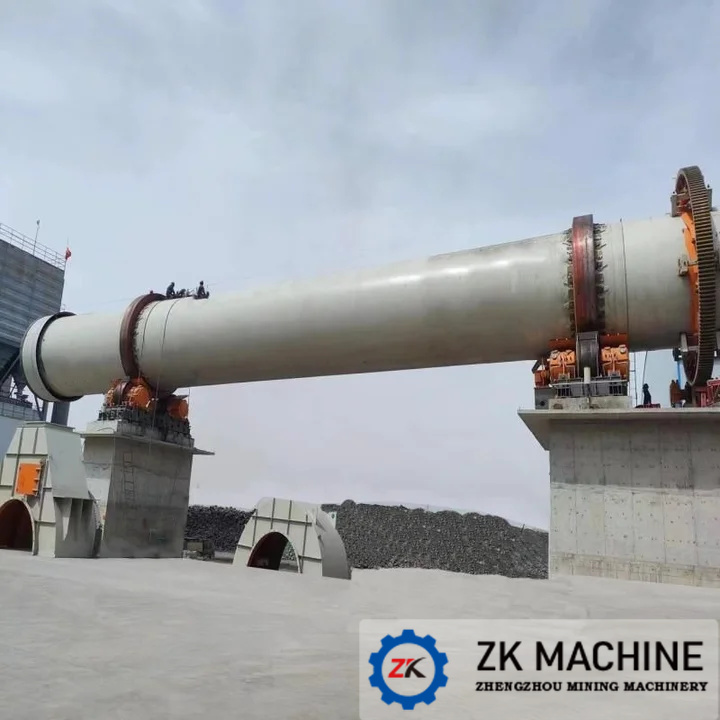